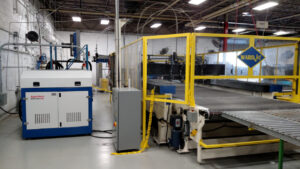
Often applications require pieces of foam that are cut, shaped, and/or molded into a specific size or shape. These applications require custom foam fabrication as the most efficient solution. Designing and manufacturing the right piece of foam yields a better quality product and much better performance in an application. Manufacturers look to custom foam fabricators like Rogers for their fabrication expertise and the state-of-the-art technology they use to create custom foam solutions.
It is important to understand the terms used in foam fabrication. Please use this short “glossary” to help you decipher the meaning and uses behind these common foam fabrication terms.
Precision Water Jet Cutting
Water jet cutting uses a high-precision, pressurized water stream to cut and carve foam into specific shapes. This non-abrasive means of cutting is a cost effective solution for material stacking.
High Speed Die Cutting
High speed die cutting is used to accurately cut and mass produce pieces of foam in various shapes. Die cutting can also be used to cut shaped holes into sheets of foam.
Vertical and Horizontal Contour Cutting
Contour cutting is a method to quickly and automatically cut patterns and complex shapes of foam. This is an ideal technique for intricate cuts and detailed shaping in foam.
Abrasive Wire Cutting
Abrasive wire cutting is used for cutting contours in various closed cell foam types. Planks or slabs of foam can be accurately cut into a variety of different configurations for a range of specific applications.
Convoluting
Convoluting is a method of altering the surface of a piece of foam. Easily recognized egg crate foam that is used in packaging, storage, and cushioning applications is a good example of this technique.
CNC Routing
Computer numerically controlled (CNC) routing uses guided drill bits and machine tools to cut and carve foam into different shapes. This technologically advanced technique allows for foam to be cut into complex shapes at multiple depths.
Vacuum and Roll Skiving
Skiving allows for very dense closed cell foams to be cut with precision and ease without wearing down the materials. Often, foam sheets can be fed into machines and cut to various thicknesses using this technique.
Foam Lamination
Laminating foams attaches two foams together for the creation of composite materials that are made from two or more types of foam. This gives pieces of foam unique characteristics like increased heat and corrosion resistance or ESD properties. Foam can also be laminated into buildups (case inserts, end caps, and the like) utilizing different lamination methods such as hot glue, spray glue, hot air, chemical bond and robotic gluing.